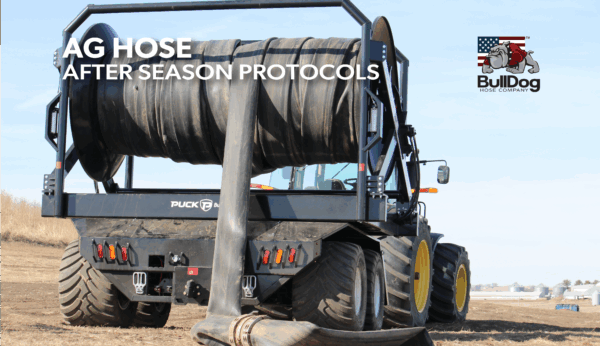
Ag Hose After Season Protocols
Over the last three years, rising costs have impacted bottom lines for businesses worldwide. Manure applicators, specifically, have seen a surge in the cost of labor, materials, fuel and equipment as operational expenses continue to rise.
Producers are also dealing with the same increases, as well as a rise in the market price of commercial fertilizer. As commercial fertilizer costs skyrocket, many producers are going back to the natural choice—manure.
With the demand for manure increasing, manure application crews know that more gallons equal a bigger payday. They also realize more gallons equate to more costs. With a little planning and time, there is a way to ensure you are maximizing the benefits of one of those expenses, and it starts before the crews ever begin rolling.
BullDog Hose Company, a division of Puck Enterprises, constructs the industry’s highest quality drag and mainline hoses. BullDog specifically engineers their hose for use in rough terrains, across many acres of land and for long hours of use on an annual basis.
The strength and performance characteristics of the hose come from a process that weaves the high-tensile yarn into a jacket, the backbone of the hose. In a through-the-weave extruding process, the hose jacket is coated with polyurethane, creating a one-piece design. As a result, a smooth inner and outer cover is formed, which greatly reduces friction loss when pumping and drag while being pulled through the field.
Joe Heese, with the sales department at Puck Enterprises, says specifying the life of mainline and drag hose is difficult as many variables come into play. “Drag hose will typically last between 30 to 50 million gallons, but the number of acres covered will determine which end of that spectrum an individual applicator falls,” he says.
Ground conditions and placement also play critical roles as stones, stubble, obstacles in the field and compression from being driven over by application crews can all negatively affect longevity.
“Probably the hardest thing on drag hose,” Heese says, “is over pulling. For example, each piece of hose is 660 feet long. Two together equals 1,320 feet. Flipping the hoses on the return would equal 2,640 feet of hose, but I would not pull more than that. Additionally, trying to compensate by going to a smaller hose with three connections for the same distance will cost gallons per minute and add more friction loss.”
According to Heese, mainline hose should last seven to 10 years, but the operator of the hose cart has the most impact on those numbers. “They should be backing into couplers and menders to prevent stress at these junction points. Pulling it straight, not twisting the hose and leaving that slack at couplers and menders adds to hose life,” Heese says.
The innovative designs of Puck Enterprises and BullDog Hose are born from real-life experiences as Puck not only manufactures and sells liquid transfer equipment, but also pumps more than 200 million gallons of manure each year. In addition, real world operation of the equipment and hoses has resulted in a set of protocols Puck applicators implement before, during, and after an application job.
Heese says the first step is to lay out and inspect all hoses. Then, mark each piece with a coded color according to the level of wear and tear. This, he adds, will help with figuring out the best use and placement of each segment. Take this time to make any necessary repairs or replace the hose if there are critical issues before heading out to the fields.
Other things that operators should do each use and/or season include:
- Test pressure on hoses, making sure it is at or below working pressure.
- Shoot a pig or bullet after each job to clean the lines as much as possible. Follow all safety guidelines.
- Do not allow hose to lay out on the ground for extended periods of time. When not in use, clean out and roll onto a hose cart.
- Again, roll that hose onto the cart carefully:
- Make sure the hose is straight when you start rolling.
- Ensure there is not an excessive amount of air trapped in the line.
- Back into couplers and menders, easing tension and bending of the hose on either side of these connections
- Store hoses out of the elements in a machine shed or barn.
Heese adds that Puck and BullDog stand behind their American made products with customer service representatives available to answer questions and help with any issues operators may be experiencing.
Want to learn more about Ag Hose After Season Protocols? The direct service line can be accessed by calling 712.655.9250.